|
Stephen Chung, Deputy Manager of Technical Support Division, Moldex3D |
Between the part designers, mold makers, tooling engineers and customers worldwide, cross-departmental discussion and collaboration are common for CAE simulation-driven projects to view the design pros and cons and share more specific identification. However, if the simulation project is shared through a regular project like Moldex3D Studio, the file size is normally large and may contain confidential information that cannot be shared with different divisions or companies.
Designed to address this issue, Moldex3D Viewer is a powerful and license-free tool used to read the analysis project developed in the new generation Moldex3D platform, Studio. It provides a variety of post-processing tools to visualize key properties and enables users to look into in-depth molding simulations. Moldex3D Viewer offers a comprehensive communication platform that helps users to enhance efficiency on design verification and optimization. The following will introduce how to use the features.
Tools provided in Moldex3D Studio and also available in Moldex3D Viewer
Step 1. Complete a simulation project with analysis results on Studio (a sample of Solid IM is used in this case) On the Project Tree, right click on the project name to open the Edit Project menu. Click on Export for Viewer to open export wizard.
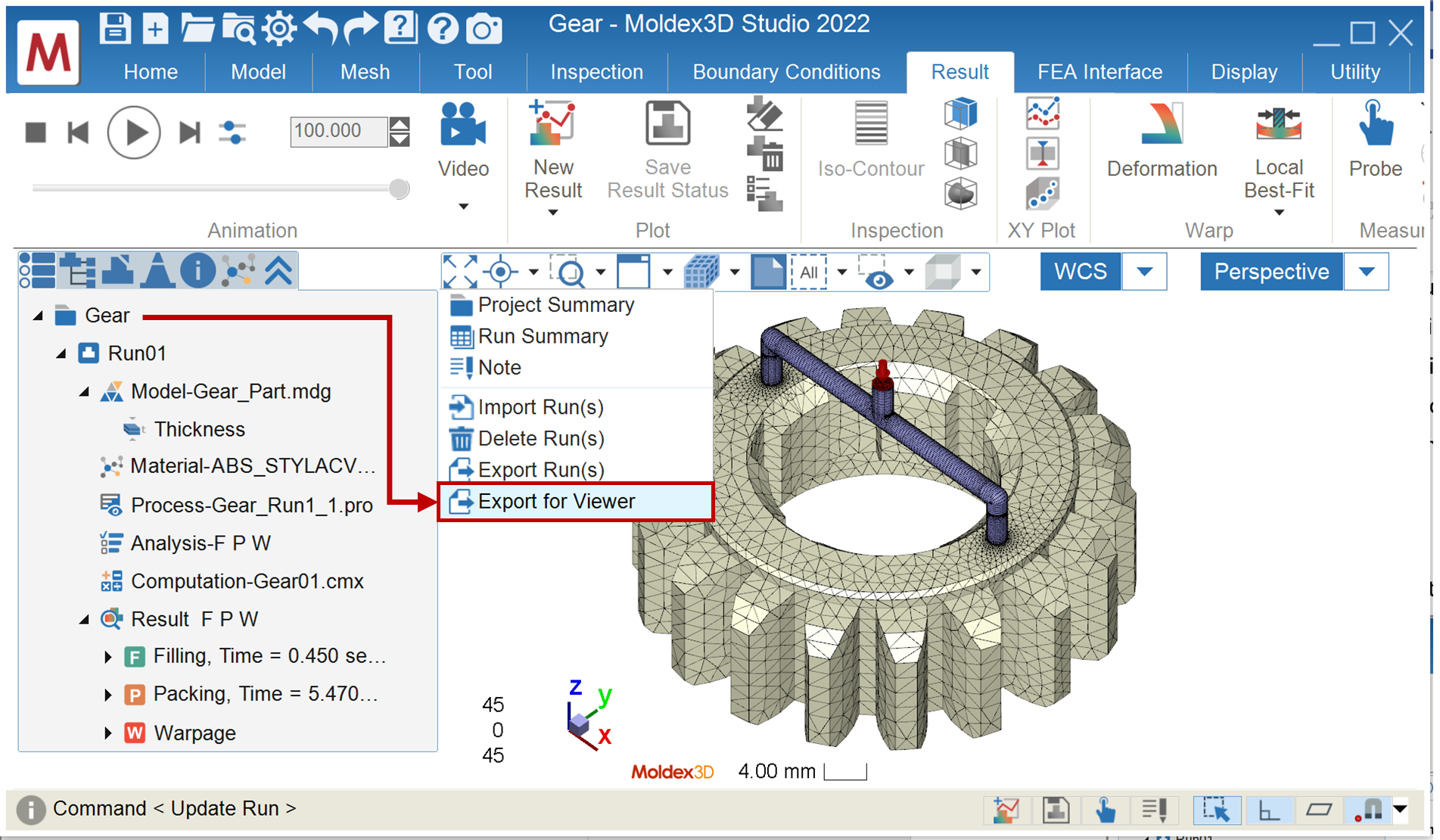
Step 2. In wizard, specify the Name and Location to save the file for Moldex3D Viewer. Confirm the other export options and click Export to start generating a Viewer file (*.mrmv). After the data export is complete, two additional buttons will appear as shown below, so one can click to open the target folder or directly open the file with Moldex3D Viewer installed.
Note: In the Run list, one can modify detailed settings of whether to export specific analysis results and time step or not.
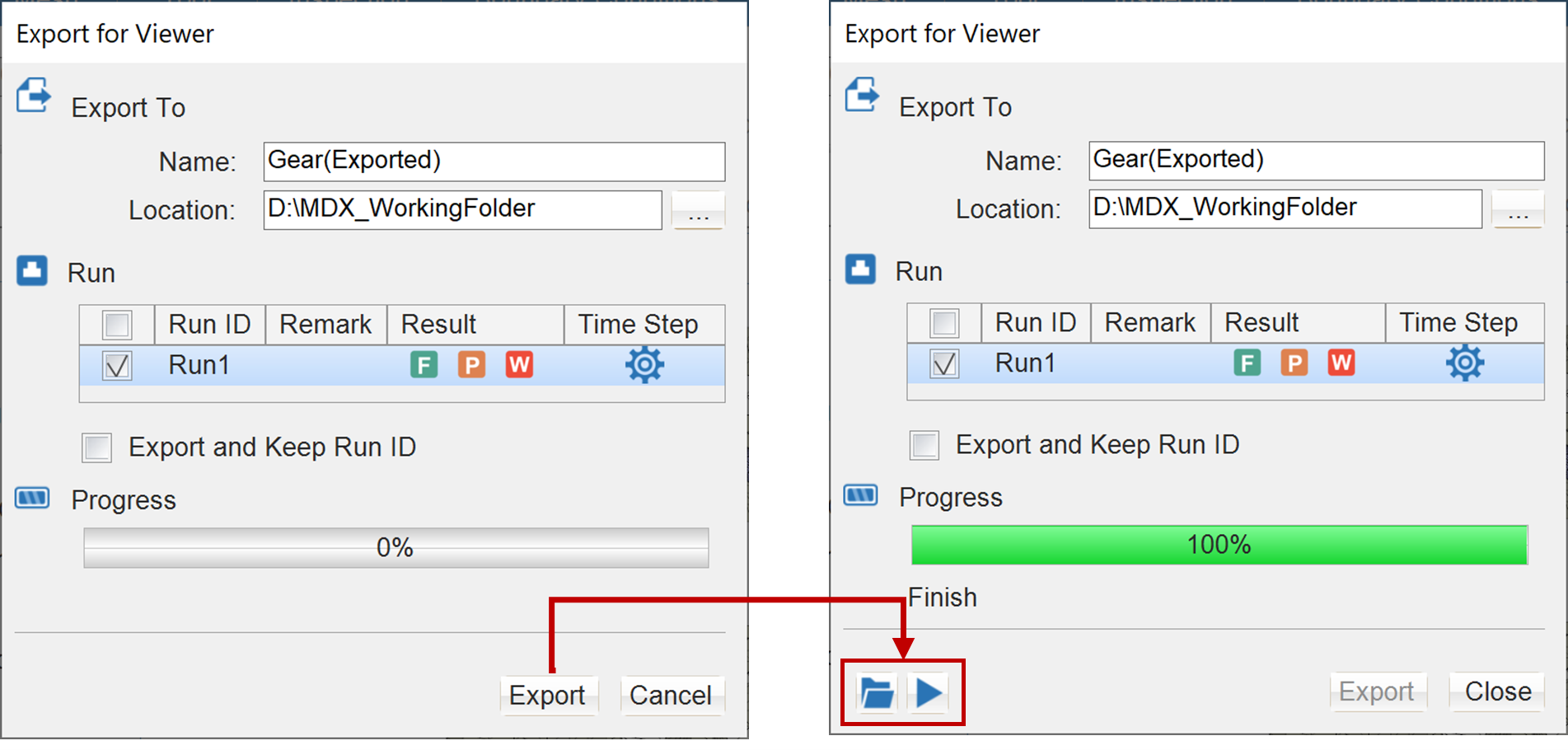
Step 3. Share the exported Viewer file to another machine that has Moldex3D Viewer installed. One can see the size of the application is reduced from 15GB (Studio) to only about 300MB (Viewer) and the size of project is reduced from 152MB (*.mrm, with many folders & files) to 73MB (*mrmv, single portable file)
Note: Moldex3D Viewer is included as an optional item of the standard install package. Also, one can download individual packages specifically for Viewer installation on Moldex3D official website.

Step 4. Launch Moldex3D Viewer and pull in the exported Viewer file, and one can see that the tabs are less than the project opened in Studio. Only post-processing tools are provided, and all project settings are for viewing only. One can then demonstrate simulation results and analysis data to collaborate with full Studio post-processing tools without installing the whole Moldex3D application.
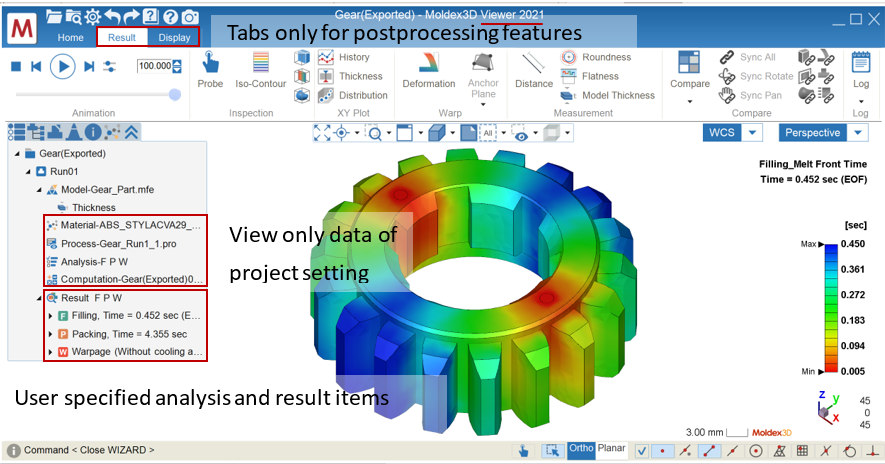
CNC Hardening System
The CNC quenching system is a highly automated heat treatment equipment that utilizes computer numerical control (CNC) technology to accurately manage the temperature, time, and cooling rate during the quenching process, in order to change the microstructure of metal materials and enhance their hardness, wear resistance, and fatigue resistance. This system is widely used in fields such as mechanical manufacturing, automotive, aviation, and tool steel, and is crucial for improving product performance.
working principle
Numerical control quenching systems usually use induction heating or bath quenching for heating. Induction heating generates eddy currents through electromagnetic induction, rapidly heating metal workpieces above the critical temperature, and then immediately immersing them in quenching media (such as oil, water, or salt solution) for rapid cooling. Bath quenching is the process of preheating the workpiece to a certain temperature and then immersing it in a low-temperature medium for hardening.
system composition
Heating unit: induction coil or heating bath.
Cooling unit: quenching medium and circulating pumping system.
Numerical Control System: Control parameters such as heating temperature and cooling rate.
Workpiece loading and transport mechanism: Ensure precise positioning and movement of the workpiece.
Security protection: monitoring and emergency shutdown mechanism.
Key advantages
Precise control: Setting the quenching path and parameters through software programming, with good repeatability.
Improving quality: uniform hardening, reducing the risk of deformation and cracking.
Energy saving and efficient: fast heating and cooling, saving energy.
Flexible production: adaptable to different specifications and batch sizes.
Automated operations: reduce manual intervention and improve productivity.
Application Cases
Automotive components: wear-resistant parts such as gears, crankshafts, connecting rods, etc.
Aerospace: hardening of high-temperature alloys and lightweight alloys.
Tool manufacturing: cutting tools, mold steel.
Medical equipment: Enhanced treatment of surgical instruments.
Military equipment: firearm components, armor materials.
Technology Trends
With the development of intelligent manufacturing, CNC quenching systems are integrating more advanced technologies, such as machine learning algorithms to optimize quenching processes, sensors to monitor material properties in real-time, and personalized customization. At the same time, we will develop efficient cooling media and improve quenching trajectory planning to further enhance quenching quality and reduce costs. In the future, highly integrated one-stop quenching production lines will become the mainstream of the industry, bringing revolutionary changes to metal processing.
Surface quenching, CNC quenching equipment, heat treatment, high-frequency quenching machine, heating system, quenching machine tool
Ningbo Dedao Electronic Technology Co., Ltd , https://www.nbdedao.com